A tractor clutch is a mechanical device used on tractors and other agricultural machinery to engage or disengage power transmission between the engine and transmission. The clutch plays a vital role in controlling the flow of power from the engine to the driveline, allowing the tractor to start, stop and change gears smoothly. The tractor clutch manufacturer will give you a detailed introduction from the following aspects:
Tractor clutch types
Tractor clutch features
Tractor clutch principle
Tractor clutch replacement
Tractor clutch maintenance
Tractor clutch types
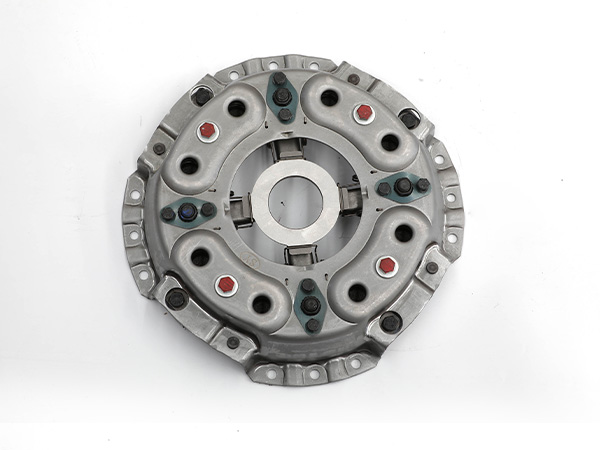
Tractors use different types of clutches based on their design, application, and power transmission requirements. The two main types of clutches found in tractors are mechanical clutches and hydraulic clutches. Additionally, some modern tractors may use a combination of these technologies.
Mechanical Clutches
- Single Plate Dry Clutch: This is the most common type of mechanical clutch used in tractors. It consists of a single friction plate and a pressure plate. When the clutch pedal is engaged, the pressure plate is released, allowing the friction plate to disengage from the flywheel, interrupting power transmission. When the clutch pedal is disengaged, the pressure plate engages the friction plate, restoring power transmission.
- Multiple Plate Clutch: Some larger tractors or those designed for heavy-duty applications may use multiple plate clutches. These clutches have multiple friction plates interleaved with steel plates, providing greater torque capacity.
Hydraulic Clutches
- Hydraulic Wet Clutch: In this type of clutch, oil is used to transmit power and cool the clutch components. It often consists of multiple friction plates immersed in oil. When the clutch is engaged, hydraulic pressure separates the plates, allowing for power transmission. Hydraulic clutches are known for smoother engagement and better heat dissipation.
Combination Clutches
- Dual Clutch Systems: Some modern tractors use a combination of mechanical and hydraulic clutches in a dual clutch system. This system often includes two separate clutches in a single housing – one for the high range and the other for the low range. It allows for seamless shifting between ranges without interrupting power delivery.
- Power Shuttle Clutch: Tractors equipped with power shuttle transmissions may have a separate clutch for controlling the direction of travel. This clutch allows the operator to shift between forward and reverse without using the main clutch. It improves operational efficiency, especially in applications requiring frequent changes in direction.
More tractor clutch types can be found: What are the types of tractor clutches?
Tractor clutch features
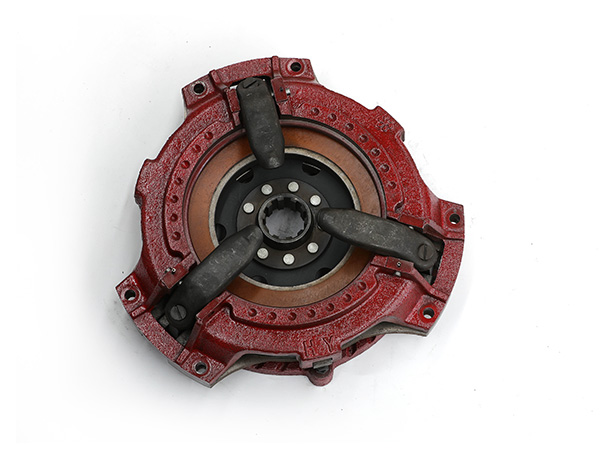
Single vs. Dual Clutches
- Single Clutch: Found in older tractors, a single clutch controls both the engine and transmission.
- Dual Clutch: Common in modern tractors, a dual clutch system consists of two separate clutches—one for the engine and one for the transmission. This design allows for smoother operation and more efficient power transfer.
Clutch Pedal
- The clutch pedal is the foot-operated mechanism used by the tractor operator to engage and disengage the clutch. It is typically located on the left side of the driver’s seat.
Clutch Disc
- The clutch disc is a friction disc located between the flywheel and the pressure plate. It engages with the flywheel when the clutch is engaged and disengages when the clutch is depressed.
Pressure Plate
- The pressure plate is a component that applies pressure to the clutch disc, allowing it to engage with the flywheel. It is released when the clutch pedal is depressed.
Flywheel
- The flywheel is a rotating disc attached to the engine’s crankshaft. It provides inertia and helps smooth out fluctuations in engine speed.
Release Bearing (Throw-out Bearing)
- The release bearing is a part of the clutch linkage that disengages the clutch when the clutch pedal is depressed. It reduces friction between the pressure plate and the release levers.
Clutch Housing
- The clutch housing encloses the clutch components and provides a protective covering for the clutch assembly.
Clutch Linkage
- The clutch linkage consists of various mechanical components that transmit the movement of the clutch pedal to the clutch mechanism, engaging or disengaging the clutch.
Adjustment Mechanism
- Some tractors have adjustable clutches to compensate for wear over time. Proper adjustment is crucial for optimal clutch performance.
PTO Clutch
- Some tractors have a Power Take-Off (PTO) clutch, which engages and disengages the PTO shaft. The PTO clutch is often separate from the main tractor clutch.
Clutch Safety Switch
- A safety feature in some tractors, this switch prevents the tractor from starting unless the clutch pedal is fully depressed, reducing the risk of unintentional movement.
Wet vs. Dry Clutches
- Wet Clutch: Immersed in oil for cooling and lubrication, these clutches are common in heavy-duty and high-power tractors.
- Dry Clutch: Operates in a dry environment without oil immersion and is commonly found in lighter tractors.
Tractor clutch principle
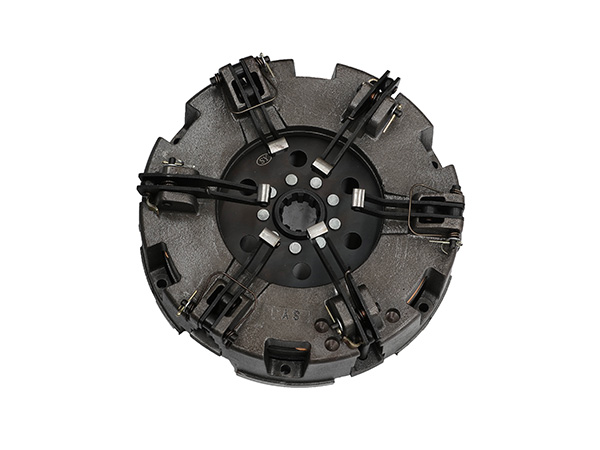
A tractor clutch is a critical component in the powertrain system that allows the engine to be connected or disconnected from the transmission. The clutch’s primary purpose is to enable smooth engagement and disengagement of power between the engine and the transmission, allowing the tractor to start, stop, and change gears without causing damage to the drivetrain.
The work principle of a tractor clutch involves the use of friction to connect and disconnect the rotating engine shaft (crankshaft) from the transmission input shaft. The specific working principles can be found in:
How does a tractor clutch work
What is the working principle of the tractor clutch assembly?
Tractor clutch replacement
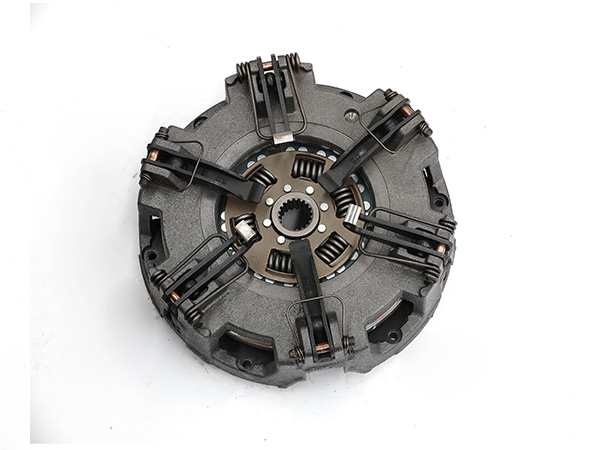
Replacing a tractor clutch involves several steps and requires some mechanical knowledge and tools. Here’s a general guide on how to replace a tractor clutch. Keep in mind that specific steps may vary depending on the tractor model, so it’s essential to consult the tractor’s service manual for accurate instructions. The specific replacement content can be found in: What is the process of replacing the tractor clutch?
Tractor clutch maintenance
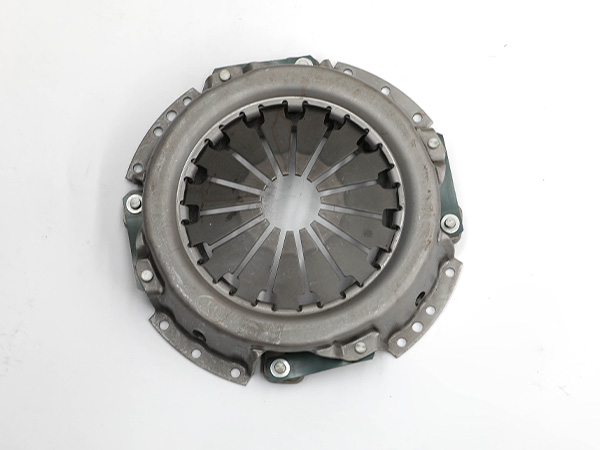
Maintaining the tractor clutch is crucial for ensuring smooth operation and extending the life of the clutch components. Here are some general guidelines for tractor clutch maintenance:
Regular Inspection
Perform visual inspections regularly to check for any signs of wear or damage. Look for oil or fluid leaks around the clutch housing.
Adjustment
Check and adjust the clutch linkage according to the manufacturer’s specifications. Proper adjustment ensures that the clutch engages and disengages correctly.
Clutch Pedal Free Play
Ensure there is the proper amount of free play in the clutch pedal. This free play is necessary for the clutch to engage and disengage smoothly. Refer to the tractor’s manual for the recommended free play measurement.
Fluid Levels
If your tractor has a hydraulic clutch, check the hydraulic fluid levels regularly. Low fluid levels can lead to poor clutch performance. Top up the fluid as needed with the recommended hydraulic fluid.
Fluid Quality
Check the condition of the hydraulic fluid. If the fluid is dirty or contaminated, it may affect the clutch performance. If necessary, flush and replace the hydraulic fluid according to the manufacturer’s recommendations.
Clutch Slippage
If you notice the clutch slipping (engine RPM increases without a corresponding increase in tractor speed), it may be a sign of wear. Address clutch slippage promptly to prevent further damage.
Clutch Housing Inspection
Inspect the clutch housing for any signs of oil leaks. Oil contamination can lead to clutch slippage and reduced performance.
Alignment
Ensure proper alignment of the clutch components. Misalignment can cause premature wear and affect the overall performance of the clutch.
Operating Techniques
Train operators on proper clutch usage techniques. Discourage habits like “riding the clutch” or excessive slipping, as these can contribute to premature wear.
Manufacturer Guidelines
Follow the tractor manufacturer’s recommended maintenance schedule and guidelines for the specific clutch system installed on your tractor. This information is typically found in the tractor’s manual.
Professional Inspection
If you notice any significant issues or if the clutch is not performing as expected, consult a professional mechanic for a thorough inspection and necessary repairs.
More tractor clutch maintenance can be found here:
YTO tractor clutch maintenance tips
What are the maintenance methods of tractor clutches
To summarize, tractor clutch selection depends on factors such as tractor size, application, and required functionality. Mechanical clutches are common on smaller and simpler tractors, while larger and more advanced tractors may be equipped with hydraulic or combination clutches to meet the needs of heavy-duty applications and provide smoother operation.